The Kingdom of Clay Pots
Vietnamese cuisine boasts numerous delectable dishes cooked in humble earthenware pots. From the fragrant golden crust of claypot rice (cơm niêu) to tenderly braised meat and fish simmered to perfection after hours on the stove, to the richly flavored caramelized fish sauce (kho quẹt) for dipping freshly boiled vegetables, these dishes embody the essence of traditional Vietnamese cooking. While the rustic clay pot is a symbol of rural cuisine, few realize that many regions across the country rely on clay pots crafted in the distant Western regions of Nghe An province.
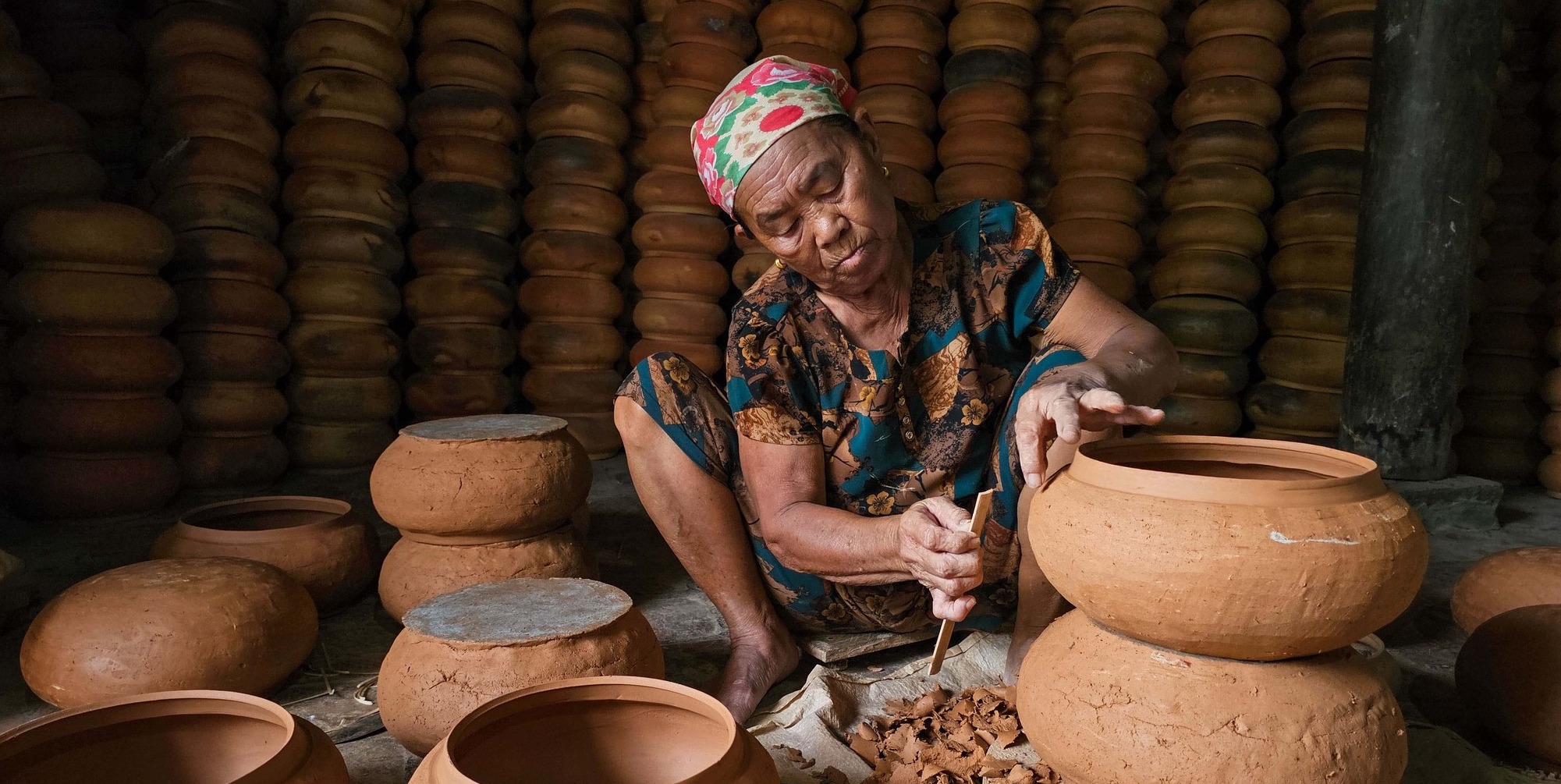
Tru Son village, nestled in Nghe An’s Do Luong district, boasts a longstanding tradition of crafting clay pots renowned for their beauty and durability. Beyond agriculture, the locals have upheld this artisanal craft for centuries, earning the village the affectionate moniker: “The Kingdom of Clay Pots.” Today, several dozen families across various hamlets within Tru Son village continue this ancestral craft, skillfully molding clay into pots and jars. Notably, the famous braised fish of Vu Dai village in Ha Nam province is traditionally prepared in clay pots from Tru Son village.
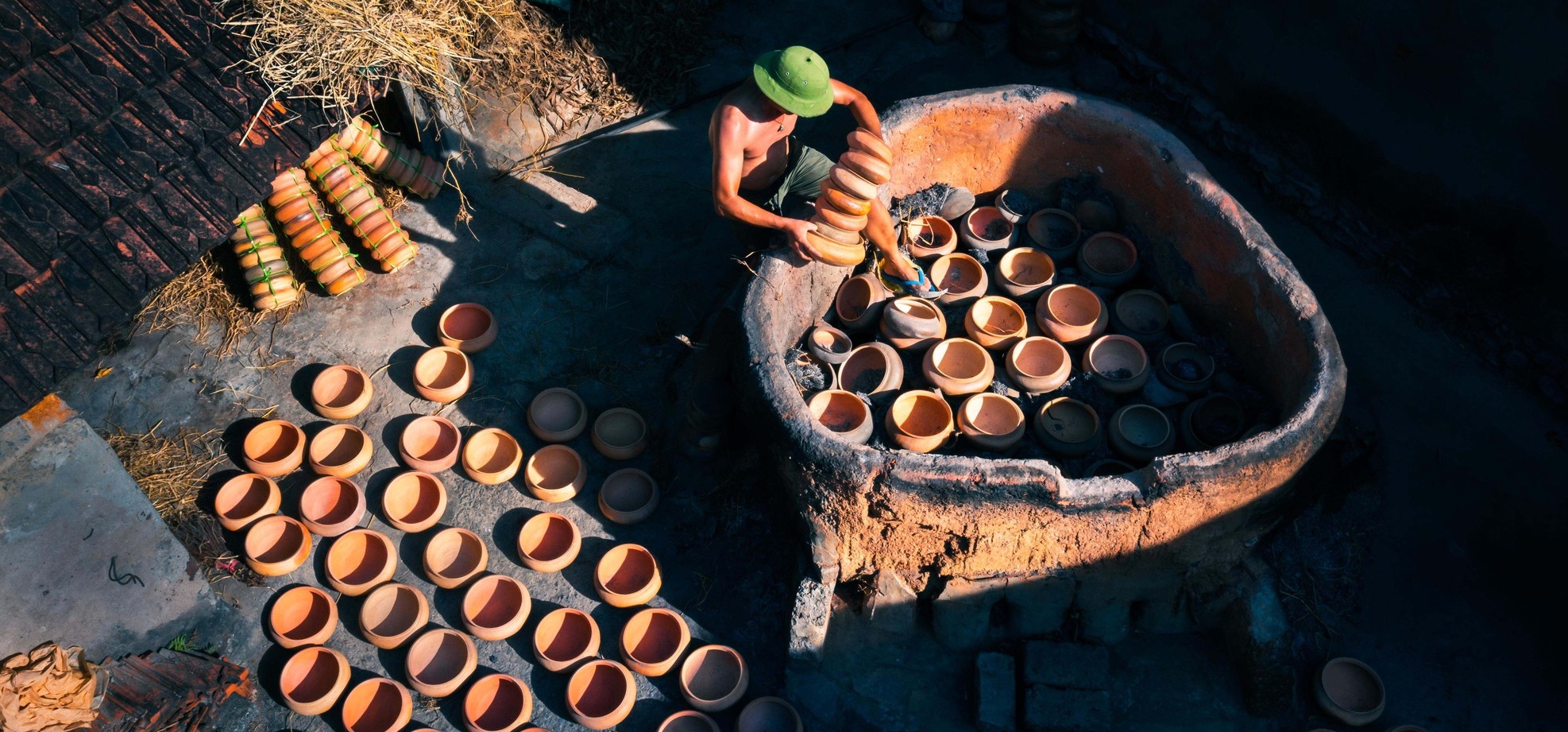
While village elders don’t know the origins of Tru Son’s pottery craft, it has been a cherished family trade for generations. Children as young as five are taught basic techniques by their parents and grandparents. Traditionally dominated by women, the craft of pottery-making was passed down from mothers and grandmothers to their daughters and daughters-in-law, as their nimble hands and patient natures were deemed ideal for this task. Even today, visitors to Tru Son will encounter women shaping clay with their soft hands, leaving a lasting impression. However, men also play significant roles in various stages of production.
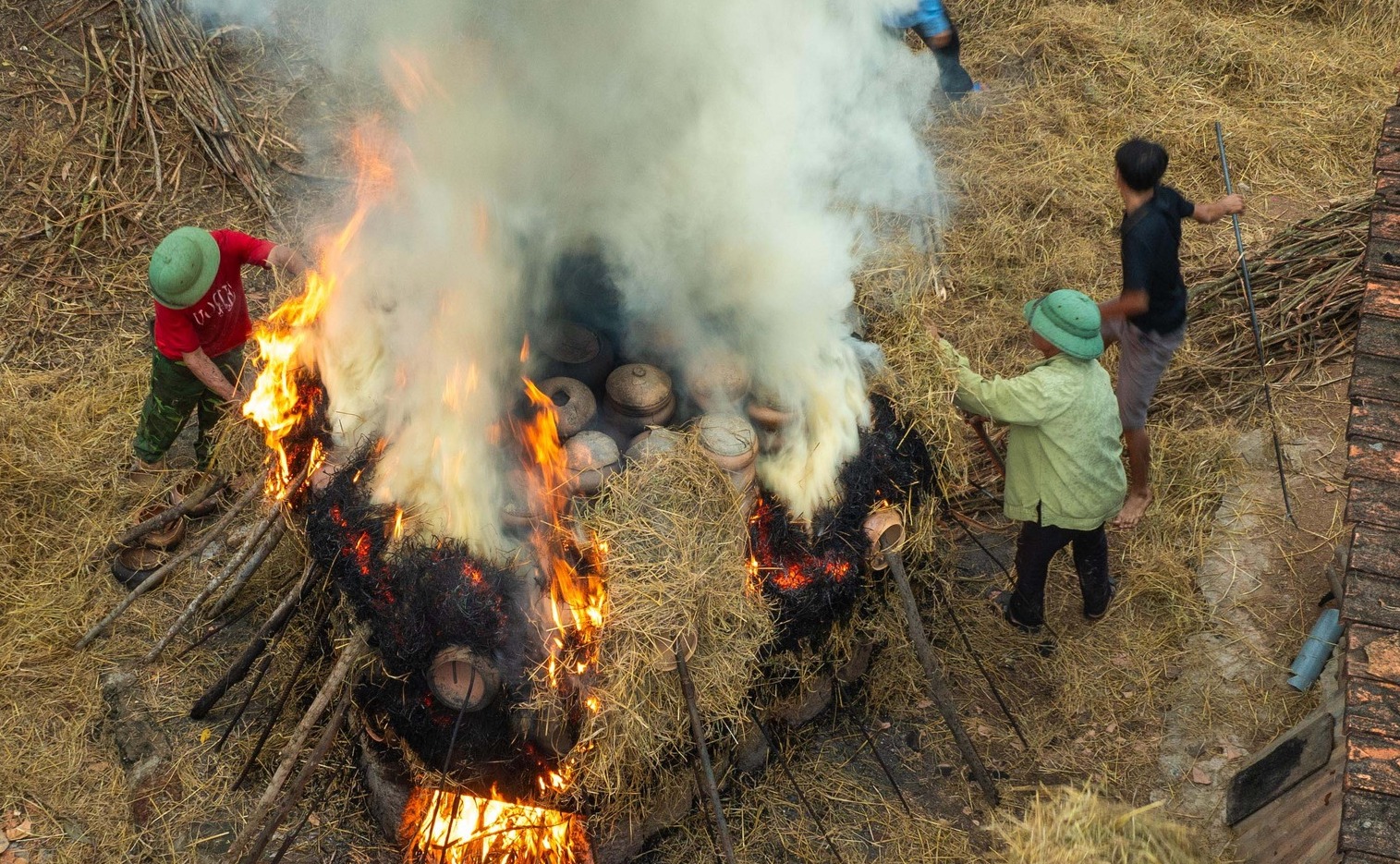
Crafting a clay pot entails multiple careful steps. The clay is meticulously prepared, kneaded, and shaped into the desired form on a potter’s wheel, then left to dry in the sun before undergoing the crucial firing process. Firing involves expertly stacking the pots in a kiln, covering them with straw or dry pine boughs, and slowly heating them from below, engulfing the entire kiln in smoke. This process lasts about 30 minutes and is repeated several times over four or five hours to achieve the desired durability and color. Firing demands precise control of smoke, fire, and temperature.
The drying and firing stages are conducted outdoors and require ample sunlight. Thus, despite the presence of modern houses, old homes with sunny yards dedicated to drying and firing pots still dot Tru Son’s landscape. Ox carts are used to transport these earthenware goods to distant provinces for sale.
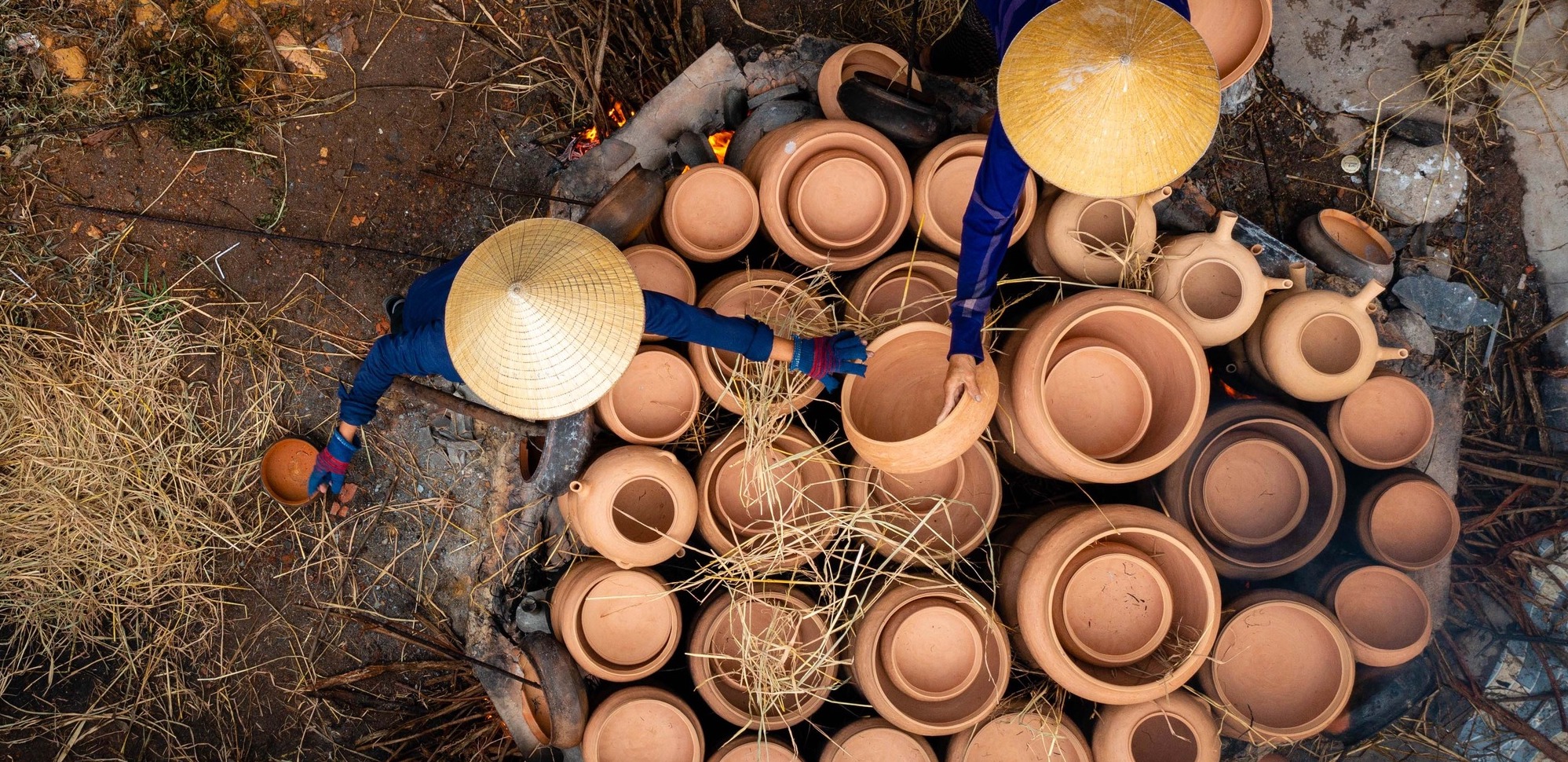